
Product Idea incl. Technology
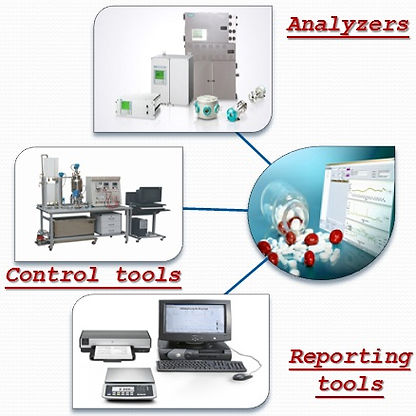
PAT is currently recommended by the Food and Drug Administration guideline but later it can be presumably obligated for companies. It supports the widely used Good Manufacturing Praxis (GMP) industrial standard from the Quality by Design (QbD) principles as far as the online release.
The Food & Drug Administration (FDA) issued the Process Analytical Technologies guidance in its final form in September 2004 when international initiation documents were accepted.
What were the reasons of the initiations?
- The pharmaceutical production is not efficient and is expensive.
- The regulation is an obstacle for continuously improving (every change means obligatory
announcement to authorities).
- The modern quality management didn’t spread like in case of other industry fields’
development (i.e. electronic industry, car industry, plane-maker industry).
- The authorities are overloaded (inspections, evaluation of registration documents).
As result, new notions became accentuate:
- Process understanding
- Quality by design
- Process analytical technology
The FDA is convinced that PAT will encourage innovation in pharmaceutical manufacturing and quality assurance. The PAT methodology is not mandatory yet, but will probably set the regulatory standard-reference in the pharmaceutical industry in the coming 5-10 years.
PAT is a system for designing, analyzing and controlling and so thus improving manufacturing processes based on timely measurements (e.g. during processing) of critical quality and performance attributes of raw materials, in-process materials and processes with the goal of ensuring final product quality. PAT allows real time follow-up of the product quality and enhances increased process understanding.
Advantages of using PAT in the biotechnological developments and during the production process:
- It is possible to identify each critical source of process deviations.
- Managing of process deviations with process regulation.
- Precise and definite forecasting of product quality parameters.
- Better process-understanding (advantage in case of technology transfer, scaling up and down)
- Process regulation can be extended by new on-line measuring technologies (i.e. Near-Infrared Spectroscopy, on-line High Performance Liquid Chromatography).
Benefits of implementing PAT:
1. Reduces documentation, overall costs of manufacturing – less waste and rework –.
2. Improves process understanding and quality – better/more reliable quality – based on only a review of process characteristics.
3. Provides product uniformity.
4. Reduces product change-over time.
5. Meets all kinds of regulatory requirements.
6. Increases automation to improve operator safety and reduce human errors, reduce inspection time and frequency
7. Prevents rejects and re-processing.
8. Increase competitiveness.
9. The ultimate goal and major benefit of PAT is real-time product release.
We are developing a patentable, new type of Process Analytical Technologies (PAT) system to control pharmaceutical manufacturing processes better through the measurement of Critical Process Parameters (CPP) which affects the product’s Critical Quality Attributes (CQA).
By analyzing the process, our software can make a forecast about future product quality.

There are a number of tools that support PAT principles in development and manufacturing plants, such as process analyzers, process control tools and reporting tools, only to name a few. But to properly implement PAT, more is needed than just supporting tools. A software, that intelligently interprets and interconnects data generated by these quality tools (one common interface for all PAT tools; all analyzers and PAT tools can be linked into a single system architecture). A software, that installs absolute data transparency by returning correlated data back to processes, from product development onward. However, beyond these basic requirements which are also mostly accessible with the competitors’ software, the advantages of our system are:
1. It is totally customizable to meet the requirements and demands of the partners.
2. It offers a complete service in regard to biotechnological applications. It is a key point as there aren’t any types of PAT software developed for the biotech industry currently (i.e. the same PAT software is used both in the car and the pharma industry), and competitors’ software in the present are too universal and not appropriate for the sensitive pharmaceutical analytical measuring equipment.
3. The classical, rigid systems become flexible because our system adapts to given technology. Model-integrated solution:
While the competitors’ PAT system is only able to interpret, interconnect and store the results and data of the measurements of the manufacturing process, our system – due to the built-in genetic-generic algorithms and models – is able to compare the results and learn from them by itself (self-learning system), furthermore it can be used for prognoses and modeling the results of future experiments, as well. It is an utterly unique feature of our software.
4. Primarily directed to reduce costs: reduces overall costs of manufacturing, less waste and rework, reduces product change-over time.
5. Offers increasing efficiency: improves quality, provides product uniformity.
6. The system also has indirect effects:
The system increases automation to improve operator safety and reduce human errors. Simulation model can be used in the early phase of technological development and designing of experiments, so thus we can get better results in model-based identification and development.